8 cast iron
8 Cast Iron Skillet - Etsy.de
Etsy is no longer supporting older versions of your web browser in order to ensure that user data remains secure. Please update to the latest version.
Take full advantage of our site features by enabling JavaScript.
Find something memorable, join a community doing good.
( 240 relevant results, with Ads Sellers looking to grow their business and reach more interested buyers can use Etsy’s advertising platform to promote their items. You’ll see ad results based on factors like relevancy, and the amount sellers pay per click. Learn more. )
No.
Back
Rated 4.9 out of 5
279 Reviews Based on 279 reviews
Rated 4.9 out of 5
279 Reviews Based on 279 reviews
Our 8" skillet is designed to be a daily cooking companion. The smaller shape and curved interior sides promote movement and flipping, while the longer handle keeps your hands farther away from heat. Like all Smithey skillets, the interior features a smooth polished finish that when seasoned is naturally non-stick. Ideal for sides, smaller meats, and the perfect fried egg, this skillet has a natural place beside its bigger siblings on the range. Use it well.
Default Title€104,95
Product Details
Description
Our 8" skillet is designed to be a daily cooking companion. The smaller shape and curved interior sides promote movement and flipping, while the longer handle keeps your hands farther away from heat. Like all Smithey skillets, the interior features a smooth polished finish that when seasoned is naturally non-stick. Ideal for sides, smaller meats, and the perfect fried egg, this skillet has a natural place beside its bigger siblings on the range. Use it well.
Features
Satin-smooth, polished finish
Extended length handle
Holes on both sides for hanging
US Made
Dimensions & Specs
Diameter (top): 8”
Depth: 1.6”
Handle to Handle: 15”
Weight: +-3 lbs
Questions
Reviews
average rating 4.9 out of 5
Based on 279 reviews
-
5 Stars
259 Reviews
-
4 Stars
14 Reviews
-
3 Stars
4 Reviews
-
2 Stars
1 Review
-
1 Star
1 Review
98% of reviewers would recommend this product to a friend
279 Reviews
Sort by Most RecentOldestPhotos & VideosHighest RatingLowest RatingMost HelpfulLeast Helpful
Robert G. Reviewed by Robert G.
Verified Buyer
I recommend this product
Rated 5 out of 5
Review posted
Best eggs over easy pan
I love having eggs made "just right" and this pan does the magic act. It has the ability to get them sizzling properly each and every time. The pan cooks eggs crunchy around the edges and then lets it be easy to flip them over without sticking. Thanks so much for this beautiful pan. The fit and finish is better then any other cast iron pan in my collection with a great balance and handle. I look forward to adding more sizes in the future.
Loading...
Was this helpful?
Joseph T. Reviewed by Joseph T.
Verified Buyer
I recommend this product
Rated 5 out of 5
Review posted
A Dream Come True
It is the perfect pan for a morning omelette. The smooth surface, the contour and its size are perfect for a single serving.
Loading...
Was this helpful?
Ania R. Reviewed by Ania R.
Verified Buyer
I recommend this product
Rated 5 out of 5
Review posted
Great little friend
I absolutely love this pan. Great shape and size. It made an excellent addition to my cast iron pan collection. I particularly love the unique shape. Rounded bottom allows for easy flipping and tossing.
Loading...
Was this helpful?
Evelyn C. Reviewed by Evelyn C.
Verified Buyer
I recommend this product
Rated 5 out of 5
Review posted
Chef skillet
The egg just slid from side to side in it. It's perfect!
Loading...
Was this helpful?
Mary Jane H. Reviewed by Mary Jane H.
Verified Buyer
I recommend this product
Rated 5 out of 5
Review posted
this was a gift
My nephew loves it so much. Uses it all the time. He said he got the perfect salmon sear.
Loading. ..
Was this helpful?
What is cast iron? Types of cast iron, properties and applications
- Cast iron at a glance
- Types of cast irons and their uses
- Pig iron
- White cast iron
- Gray cast iron
- Ductile iron (modified)
- Malleable iron and its markings
- Special cast irons
- How do special impurities affect the structure of cast iron?
- Advantages and disadvantages
- Weldability of cast irons
- Iron production volumes
- What is cast iron made from and where is it used?
Cast iron is an iron-carbon alloy with a carbon content of more than 2.14%. It may also contain permanent impurities, and sometimes alloying components. Its mechanical properties depend on the structure and mainly on the form in which the carbon is found, and the main structural constituents are cementite or graphite and austenite decomposition products, which, depending on the cooling rate, can be martensite, troostite, sorbite, perlite and ferrite. The introduction of various alloying elements makes it possible to control the graphitization process and adjust the properties of cast iron in different ways.
Cast iron at a glance
Steel and cast iron are common technical terms for alloys of iron and carbon. The carbon content in cast iron is from 2.14% to 6.67%, the rest is iron, impurities and alloying additives. Carbon can be in the form of graphite or cementite (Fe 3 C - cementite, iron carbide) inclusions. The main impurities are silicon, sulfur, manganese and phosphorus. Cast iron is used in foundry production, and is also used as a raw material for steel smelting.
Characteristics and classification of cast irons
The characteristics of the alloy are formed at the production stage. Depending on the parameters of the eutectic transformation, cast irons are gray (carbon in the form of graphite), white (carbon in the form of cementite) and half cast irons.
The size and configuration of graphite inclusions determine the grades of cast iron and their application. According to the shape of graphite inclusions, they are subdivided into cast irons with lamellar, spherical, vermicular and flaky graphite, and according to the type of metal base - into pearlite, pearlite-ferritic, ferritic, austenitic, bainitic and martensitic. In addition to carbon, cast iron contains:
- sulfur - 0.02-0.2%;
- silicon - 0.5-3.6%;
- manganese - 0.2-1.5%;
- phosphorus - 0.04-1.5%.
Depending on the content of additional additives, cast irons are divided into unalloyed and alloyed. Alloyed alloys include alloys in which elements such as nickel, chromium, copper, aluminum, titanium, vanadium, tungsten, molybdenum, etc. are added to create specific properties. In turn, alloyed cast irons are classified according to the main alloying into chromium, aluminum, nickel, etc.
The main differences between steel and cast iron
The main difference between cast iron and steel is the proportion of carbon in their composition (in steel it ranges from 0. 025% to 2.14%, in cast iron - over 2.14%) and the content of impurities (there are more of them in cast iron). This forms the melting point of the alloys. If for cast irons it is 1150-1250 degrees, then for steels this figure reaches 1500 ° C.
Steel will be lighter in appearance, while gray cast irons will have a dark and matt finish. Steel is easier to weld and forge, but worse for casting. A cast iron product has a slightly higher thermal conductivity than a steel product.
Manufacture of iron castings
Types of cast iron and their applications
Pig iron
This alloy is smelted in blast furnaces and is intended for further processing into steel or castings. Can be used in both liquid and solid state. In pig iron, the content of silicon, manganese, sulfur and phosphorus is strictly controlled. The main standard that specifies the requirements for these products is GOST 805. Depending on the silicon content and purpose, the following types of pig iron are distinguished:
- Pig iron for steelmaking grades P1, P2;
- pig iron for foundry production grades PL1, PL2;
- phosphorous pig iron PF1, PF2, PF3;
- pig iron PVK1, PVK2, PVK3.
White cast iron
All carbon in it is in the form of cementite. The structure is formed at a high cooling rate. A distinctive feature of this type of cast iron is a white tint at the fracture site, as well as high brittleness and hardness (HB 450-550). The product is practically not amenable to machining with a cutting tool. Such alloys are used for the manufacture of cast wear-resistant parts (grinding balls, screw blades, shot-blast turbine blades, rolling rolls), as well as the basis for the production of ductile iron varieties. The wear resistance of cast iron is increased by alloying with molybdenum, nickel, manganese and other elements.
Gray cast iron
In gray cast irons, carbon is represented by lamellar graphite. It is in free form, due to which the fracture has a characteristic gray color. Such an alloy is relatively well machined, has a relatively low strength and low tensile ductility. At the same time, due to the presence of lamellar graphite, gray cast iron has good antifriction and damping properties, low sensitivity to stress concentrators. The internal structure is formed at low cooling rates.
Gray cast iron has good fluidity and is less prone to shrinkage defects compared to other types of cast iron, so it is widely used for the manufacture of complex shape castings with wall thicknesses up to 500 mm.
Marking is defined by GOST 1412 and denotes a list of grades from SCh 10 to SCh 35.
- Letters SCH - gray cast iron;
- figures - information about the tensile strength (MPa / 10).
Ductile iron (modified)
The peculiarity of this alloy, obtained by adding pure magnesium (Mg), its compounds or other modifiers-spheroidizers (cerium, yttrium, etc.) to the cast iron melt, is that the graphite in such cast iron has a spherical shape. The amount of the modifying component, the same magnesium, is 0. 02–0.08%.
The properties of nodular cast iron are determined mainly by the metal base (in contrast to gray cast iron with lamellar graphite inclusions). Such a high-strength alloy is used in the production of wear-resistant parts for critical purposes that can withstand large static, cyclic and impact loads under wear conditions, including in aggressive environments and at high temperatures.
GOST 7293 regulates the requirements for the chemical composition and properties of alloys with nodular graphite for castings. In accordance with this standard, products of grades VCh 35, VCh 40, VCh 45, VCh 50, VCh 60, VCh 70, VCh 80 and VCh 100 are produced, where "VCh" is the designation of ductile iron, and the number is the minimum value of the temporary resistance σv ( MPa/10). Thus, the product HF 40 has σv not less than 400 MPa. Ductile irons are on a ferritic, ferritic-pearlitic, pearlitic basis.
Ductile iron and its designation
An annealed product of white cast iron blanks containing graphite in the form of flakes (“annealing carbon”) in its structure. This gives the alloy high strength and increased ductility, uniform distribution of properties, good machinability and almost complete absence of internal stresses in castings. Due to these properties, malleable cast iron has found application in the production of critical products - parts and elements operating under vibration and shock loads.
Depending on the chemical composition of the cast iron and the annealing conditions, it is possible to obtain a different base - ferritic, pearlitic or ferritic-pearlitic. There are also two varieties of malleable metal - black-hearted and white-hearted. The main parameters of such products are regulated by GOST 1215.
Capaciously and accurately characterizes ductile iron marking, which contains not only its designation (KCh), but also the main mechanical properties - minimum tensile strength and relative elongation For example, the alphanumeric code KCh 33-8 means that ductile iron of this brand has a minimum tensile strength of 37 kgf / mm 2 (or 323 MPa), and the elongation index is not less than 8%.
Special cast irons
There are grades of alloys with special characteristics, which are achieved by alloying, using a special annealing and cooling technology. These cast irons include:
- heat resistant;
- corrosion resistant;
- artistic;
- anti-friction and wear-resistant;
- cast irons with special electromagnetic properties;
- ferroalloys and others.
Specifications for alloyed special cast irons are regulated by DSTU 8851, GOST 7769, ISO 2892 and others. They specify what cast iron is made of for various special applications, what mechanical properties it should have and how it should be marked.
How do special impurities affect the structure of cast iron?
In the production of individual alloys, the addition of special additives to cast iron changes its composition and properties.
- Silicon is the most important alloying element in cast iron, which together with carbon influences the structure and properties.
Silicon has a positive effect on the release of graphite, improves the casting characteristics of the alloy.
- Sulfur reduces the ability of liquid iron to fill molds, reduces its mechanical properties and imparts red brittleness.
- Manganese has a negative effect on casting properties, counteracts graphitization, but increases hardness and strength.
- Phosphorus is necessary in the manufacture of cast iron castings of complex shape, including thin-walled ones, since it contributes to an increase in the fluidity of the alloy. But at the same time, strength is lost, fragility increases.
Other alloying additives introduced at the stage of material smelting also allow achieving specific properties. This results in a modified characteristic of cast iron with improved wear or heat resistance, corrosion resistance or electrical conductivity.
Advantages and disadvantages
The first discovered rough iron castings date back to the middle of the 14th century. Since then, technology has changed significantly, and the use of cast iron has expanded. Objectively evaluating this product of ferrous metallurgy, it is necessary to name both its positive and negative sides.
Undeniable advantages
First of all, it is environmental friendliness and excellent hygienic qualities. The same cast-iron cookware is not destroyed in acid-alkaline solutions, it washes well and warms up, keeping the accumulated heat for a long time. It should be noted the durability and a wide range of products, cost-effectiveness and a relatively simple process for the production of cast iron products.
By varying the state of carbon in the alloy, white or gray cast iron can be obtained. A wide range of applications is due to easy processing (forging), high heat transfer and strength.
Disadvantages of cast iron as a material
The weakest sides of the alloys are brittleness and susceptibility to rust even with short-term contact with water. In addition, cast iron products are characterized by a large weight and a specific set of physical and mechanical characteristics that require special conditions for their transportation, assembly and maintenance.
Cast iron
How is cast iron made?
The alloy is smelted in blast furnaces and cupolas. The main source of iron is iron ore raw materials, a product of ore dressing. The fuel used is coke (a product of special processing of hard coal), natural gas, pulverized coal fuel. The high-temperature technology of cast iron smelting in a shaft furnace makes it possible to start chemical reduction processes and release iron from oxides.
As a result of blast-furnace smelting, an alloy of iron and carbon is obtained - cast iron, as well as slag containing unreduced oxides, flux residues, fuel ash, etc.
Suitability of cast iron for welding serious approach. In the technological aspect, the suitability of the metal is low.
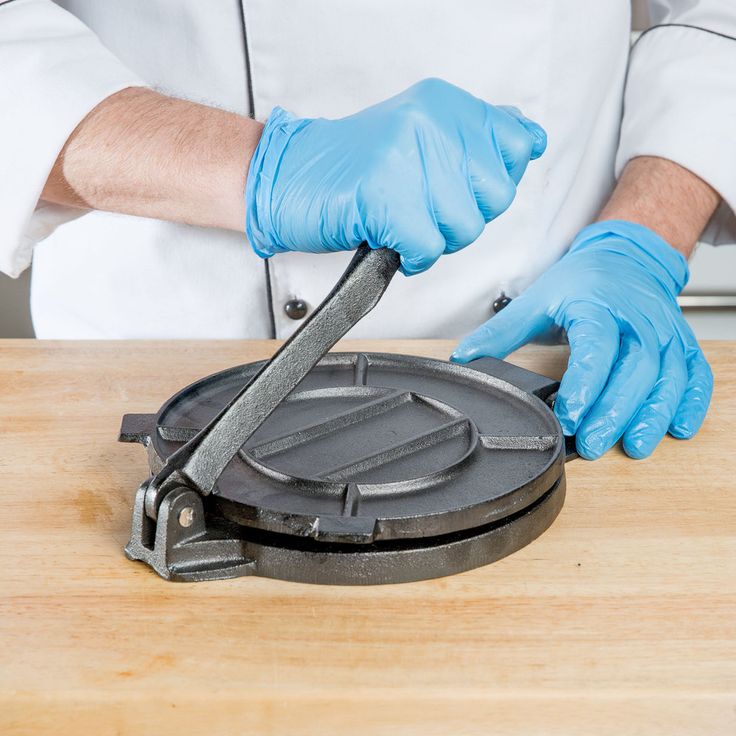
The use of cast iron for welding with metals with different cooling/heating rates results in weld cracking and brittleness. Therefore, for welding, they resort to the use of coated or carbon electrodes, flux-cored wire, and gas welding installations. The preheating of the parts to be welded and the correct choice of the welding mode helps to avoid the formation of hardened areas.
Volumes of pig iron production
The People's Republic of China has been firmly holding the first place in the world in pig iron production for several years in a row. For the first two months of 2019Chinese companies increased the volume of its production up to 126. 59 million tons. Thus, more than half of the world's pig iron is smelted in China today.
Volumes of world production of pig iron, thousand tons
In addition to China, India, Japan, Russia, South Korea, Iran, Brazil, Germany and the USA are among the top producers of pig iron. And the TOP-10 is closed by Ukraine, which became possible due to the stable activity of Metinvest Group enterprises.
Global iron production from 2010 to 2019
Region | Years | |||||||||
2010 | 2011 | 2012 | 2013 | 2014 | 2015 | 2016 | 2017 | 2018 | 2019 | |
EU | 94054 | 93 855 | 90 493 | 92 328 | 95 176 | 93 596 | 91 312 | 93 235 | 90 787 | 85 691 |
Other European countries | 9643 | 10 184 | 9 774 | 10 411 | 10 876 | 11 992 | 12 280 | 12 741 | 12 873 | 12 265 |
CIS | 77 923 | 80 174 | 81 860 | 81 962 | 79 452 | 77 585 | 82 396 | 75 952 | 75 396 | 73 938 |
North America | 39 216 | 42 159 | 44 328 | 41 319 | 41 218 | 35 859 | 33 008 | 32 946 | 34 886 | 32 567 |
South America | 34 531 | 37 535 | 30 454 | 29 992 | 30 671 | 31 627 | 29 439 | 31 654 | 31 744 | 29 087 |
Africa | 6 725 | 5 564 | 5499 | 5 778 | 5 252 | 5 264 | 5 111 | 5 152 | 5 411 | 4 266 |
Asia | 763 032 | 826 220 | 854 111 | 902 136 | 917 651 | 897 875 | 913 410 | 927 722 | 994 748 | 1 037 317 |
Middle East | 2540 | 2 242 | 2 143 | 2007 | 2 782 | 2459 | 2 251 | 2 293 | 2362 | 2530 |
Oceania | 6 672 | 5 925 | 4 381 | 4 160 | 3 962 | 4 272 | 4 313 | 4441 | 4 561 | 4 336 |
What is cast iron made from and where is it used?
The material is quite popular in mechanical engineering and other industries. It is the main component of raw materials for steelmaking in oxygen converters, open-hearth furnaces and electric arc furnaces. In addition, cast iron is the most popular alloy for making castings of various shapes. The demand for cast iron in other areas is due to its high strength characteristics and sufficient density. The areas of application of some brands are summarized in the table.
Alloys | Applications |
Gray | Manufacture of columns, flywheels, base and foundation plates, pulleys, frames, rolling machines, sewer products. |
Ductile | Bases for heavy equipment, supports of railway and automobile bridges, crankshafts for engines of diesel vehicles and tractors. |
Alloy white | Grinding parts of equipment, molds for refractories, rolls. |
Anti-friction | Plain bearings, fuel pump bushings, valve guides, automobile piston rings. |
High strength | Turbine parts, crankshafts, engines for tractors and cars, moulds, gears, rolls. |
If you are interested in high-quality rolled metal from certified materials, please contact Metinvest-SMC. In our rolled metal catalog you will find any product from more than 200 main items in the right sizes and at the right price.
Gear pump SHN7K(R)(1.8...6m3/hour)(cast iron) - OOO ITC Pishmashservis
capacity from 1.8 to 12.0 m3/h
(ShNK7 - brand of pump, working part version cast iron , R-version with heating/cooling jacket)
Photo of pump ShN7K (cast iron) - version without heating/cooling jacket
Photo of pump SHN7KR (cast iron) - version with heating/cooling jacket
APPLICATION
industry for pumping chocolate masses, chocolate icing and other similar viscous food products. Pumps can be used for pumping non-food products (in boiler rooms - for supplying fuel oil)
Viscosity of pumped products must not exceed 505 cm 2 /s, density up to 1.45 t/m 3 , in the temperature range from 20 0 C to 90 0 C.
ADVANTAGES:
Versatile design and installation and connecting dimensions for various designs;
Possibility of manufacturing with a heating jacket;
Possibility of manufacturing a pump on rolling bearings;
The low speed of rotation of the working elements significantly increases the service life of the unit.
PUMP INLET/OUTLET VERSION
vertical inlet/outlet | vertical inlet/outlet |
ГАБАРИТНЫЕ РАЗМЕРЫ НАСОСОВ СЕРИИ ШН7К(Р)
РАЗМЕРЫ ПРИСОЕДИНИТЕЛЬНЫХ ПАТРУБКОВ НАСОСОВ СЕРИИ ШН7К(Р)
ТЕХНИЧЕСКИЕ ХАРАКТЕРИСТИКИ ШЕСТЕРЕННЫХ НАСОСОВ СЕРИИ ШН7К(Р):
Pump brand | Productivity | Power electric motor , kW | Discharge pressure , MPa(atm) | Speed |
ShN7K(R)-1.![]() | 1.8 | 1.5 | 0.8(8) | 28/720 |
ShN7K(R)-2.3 | 2.3 | 2.2 | 35/940 | |
ShN7K(R)-2.8 | 2.8 | 2.2 | 45/940 | |
ShN7K(R)-3.1 | 3.1 | 3.0 | 56/1420 | |
ShN7K(R)-4.5 | 4.5 | 4.0 | 71/1420 | |
ShN7K(R)-6.0 | 6.0 | 4.0 | 90/1420 | |
ShN7K(R)-12.0 | 12.0 | 7.5 | 216/1420 |
Product temperature - up to +90 0 C
Viscosity up to 505 cm 2 /s
Mains voltage - 380 V
Shaft sealing - stuffing box packing
Material of the flow part of the pump - Gray cast iron Sch20 GOST 1412-85
Material of the pump body and frame - Gray cast iron Sch20 GOST 1412-85
Overall dimensions - 1055 x 400 x 460 mm
Weight - 228 kg
SHAFTS SEAL OF SERIES SHN7K(R)
Stuffing box packings (impregnation - silicone oil) - recommended for installation when the pump is operating at high temperatures and abrasive products.